Top Warehouse Management Metrics and KPIs
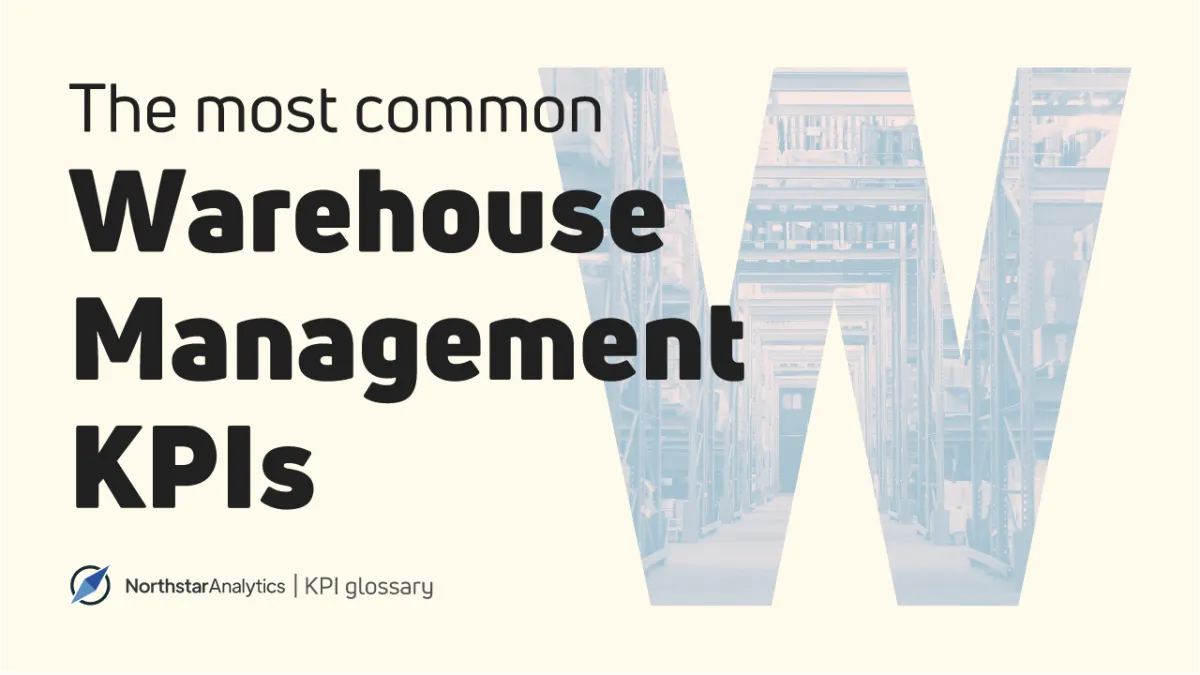
Receiving Efficiency
This statistic compares the throughput of received material to the quantity of work assigned to each employee. It is calculated as Volume of received inventory / Total number of staff hours.
Put-Away Efficiency
This is a measure of the amount of stock relocated in relation to the amount of work allocated to the operation. It is also known as put-away productivity. It is determined as the volume of stock stored divided by the number of worker hours.
Put-Away Cycle Time
The rate at which put-away activities occur is also an important statistic. Establishing a baseline provides warehouse personnel with a benchmark against which to push improvements. It is calculated as the total time spent on each put-away assignment.
Inventory Accuracy
A precise inventory count is critical to running a successful warehousing operation. This statistic ensures that the actual inventory on the warehouse floor corresponds to what is reported in the system. It is calculated as the sum of the inventory management system count and the physical inventory count.
Inventory Turnover
This KPI assists warehouse managers in determining how rapidly products move through the warehouse. In general, a faster turnover indicates a more efficient operation. Inventory turnover is determined as the total number of sales divided by the average inventory level.
Cost Per Order
Based on the type of business and industries served, each warehouse will have its own set of dynamics. The cost per order helps to measure the total cost of fulfilling orders from a specific warehouse. Total fulfillment cost / total number of orders is used to compute it.
Order Cycle Time
The order cycle time is the amount of time it takes to complete a customer order from placement to delivery. Total time from order entry to package delivery is used to calculate it.
Order Accuracy Rate
This indicator, which is expressed as a percentage, is useful for determining the overall success of order fulfillment activities. It is calculated as (Total orders correctly delivered / Total number of orders) x 100.
Picking Accuracy
This measure provides a comprehensive picture of picking effectiveness. It can be used as a baseline and monitored to see if additional workflow modifications improve or degrade these metrics. (Total orders picked error-free / Total order number) × 100 = picking accuracy.
Return Rate
Items might be returned for a variety of reasons, and it is always necessary to investigate each return separately. Measuring the overall return rate allows a corporation to determine whether or not returns are increasing or decreasing over time. It is determined as the total number of returned items divided by the total number of items shipped.